The Thuringia steelworks in Unterwellenborn has a long tradition and has developed into a modern, globally active steel producer. It stands for quality, reliability, efficiency and sustainability. As part of the SWT Green Steel Strategy, the plant is pursuing the goal of producing climate-neutral steel by 2040, with a focus on reducing CO₂ emissions through the use of electrical energy.
Challenge
The main aim of the retrofit was to reduce the energy consumption of the dedusting system by 40-60% without compromising the system’s performance. A large part of the existing system was to continue to be used. As the existing electrical rooms did not offer sufficient space, it was necessary to create new electrical rooms for the modernization.
An extremely tight time window of just 8 days was available to carry out the conversion during the scheduled summer shutdown in 2024. The complete conversion and commissioning had to be completed within this period, which required precise planning and implementation under high time pressure.
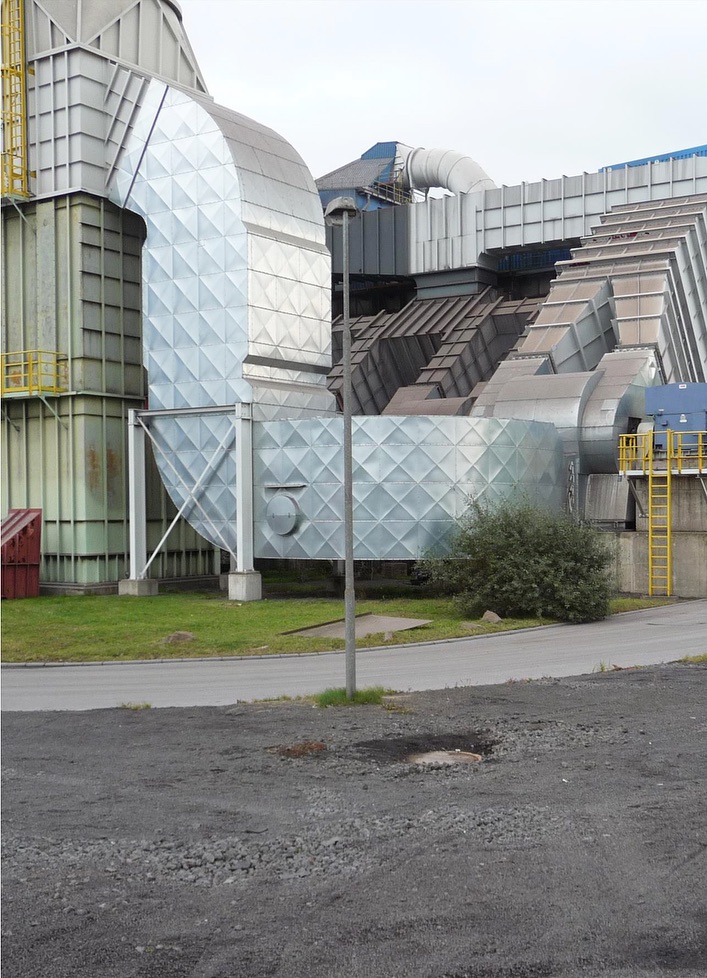
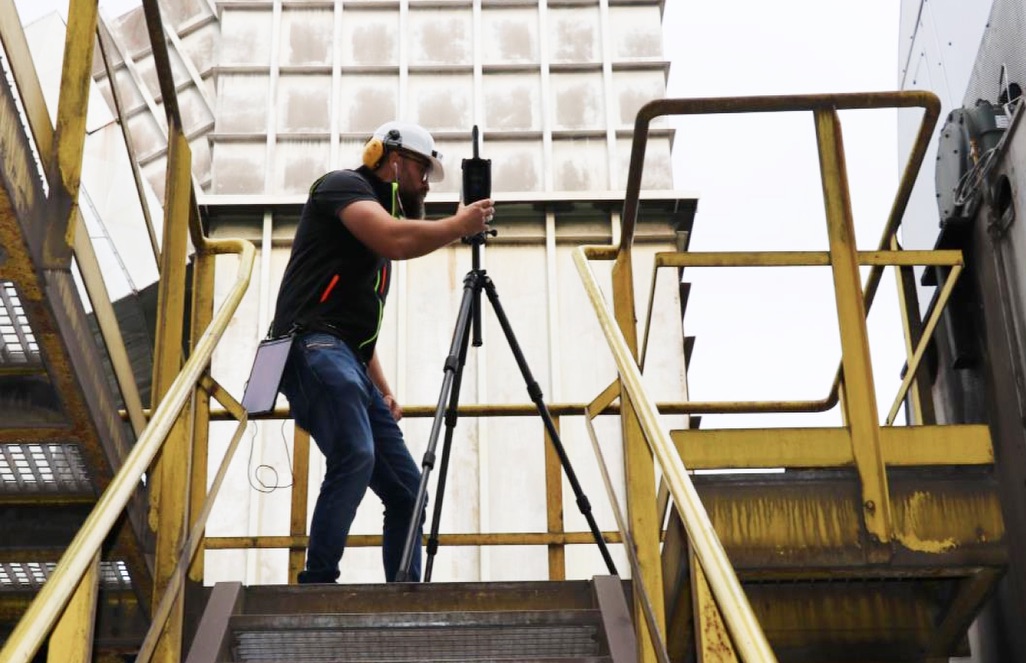
Solution
After the order was placed, Reitz Retrofit began analyzing the existing fans and ancillary equipment. An FEM analysis revealed that the rotor units had to be replaced with speed-compatible ones. These were tested using CFD analysis, and the final design met all requirements while continuing to use the old housings.
3D laser scanning was used to plan the new components precisely. This included the electrical compartments, cable routes, soundproof enclosures and the precise integration and reuse of the existing motor bases. This technique enabled detailed and efficient planning in order to make optimum use of the existing infrastructure and at the same time meet the new requirements.
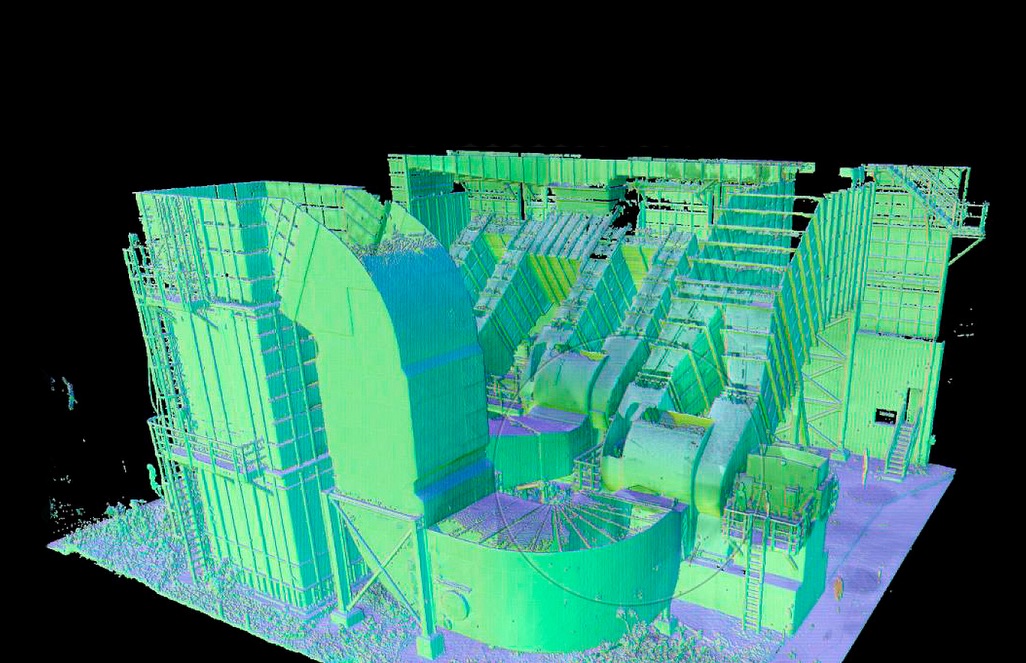
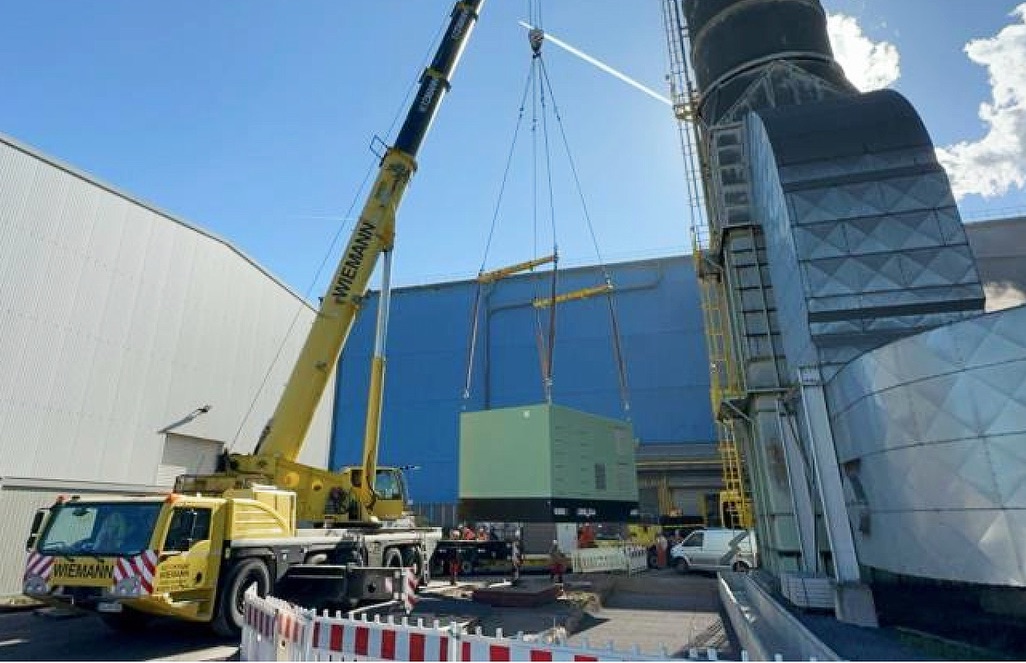
Due to the limited space available, Reitz Retrofit opted for an innovative concept with three separate electrical rooms. Each room contained a 6KV/690V transformer (2 MVA) as well as a low-voltage room for control cabinets and frequency converters. An efficient cooling system, based on a CFD analysis, keeps dust-laden air out of the electrical rooms.
In addition, noise emissions were significantly reduced by special soundproof housings for the motors. These housings not only fell below the specified limit values, but also enabled maintenance-friendly access to all internal components.
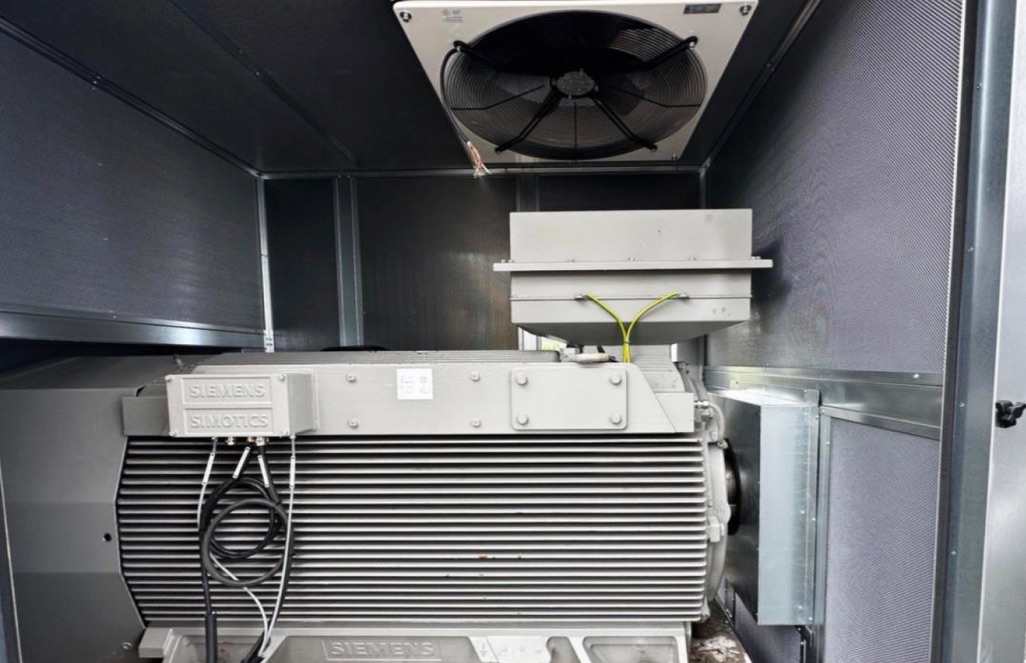
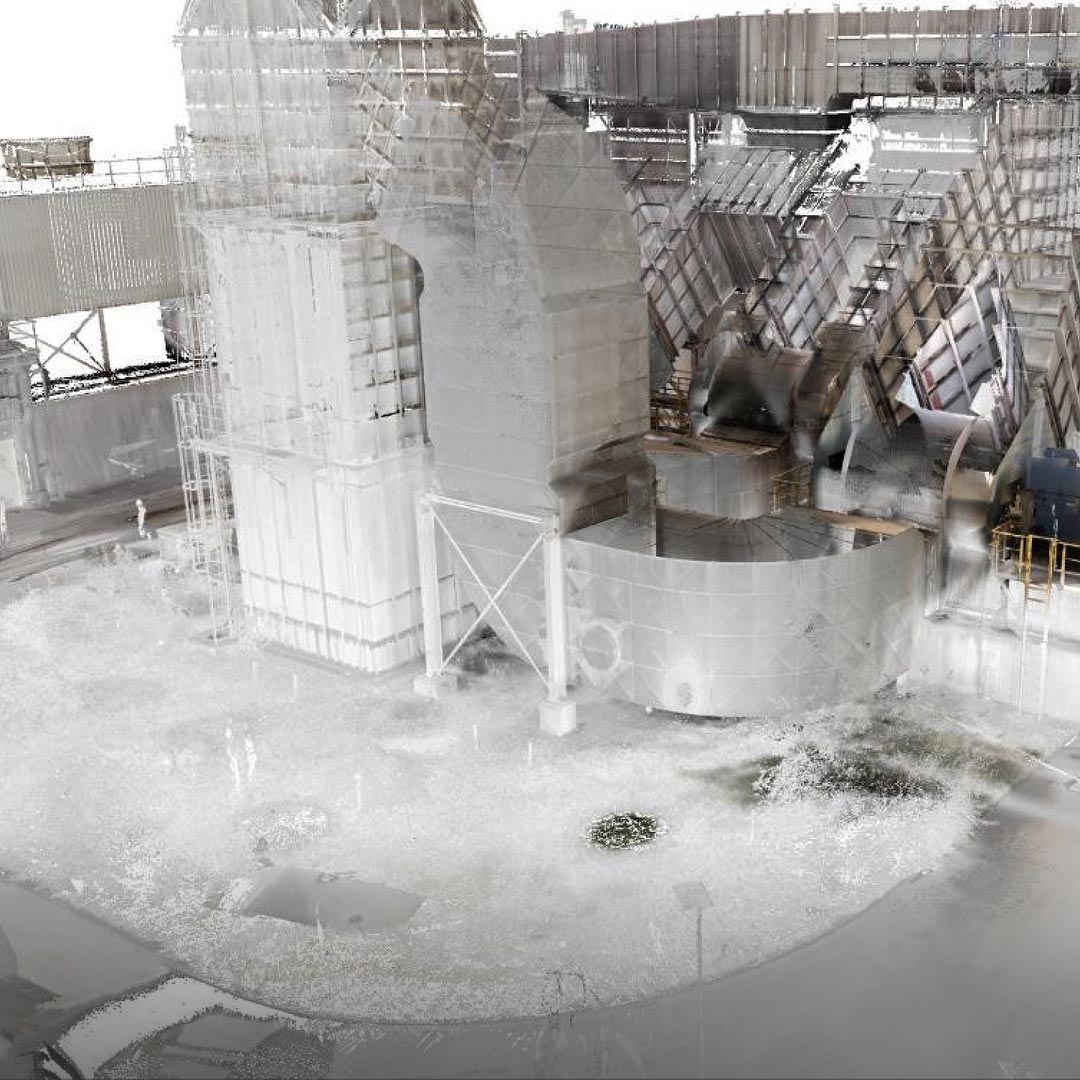
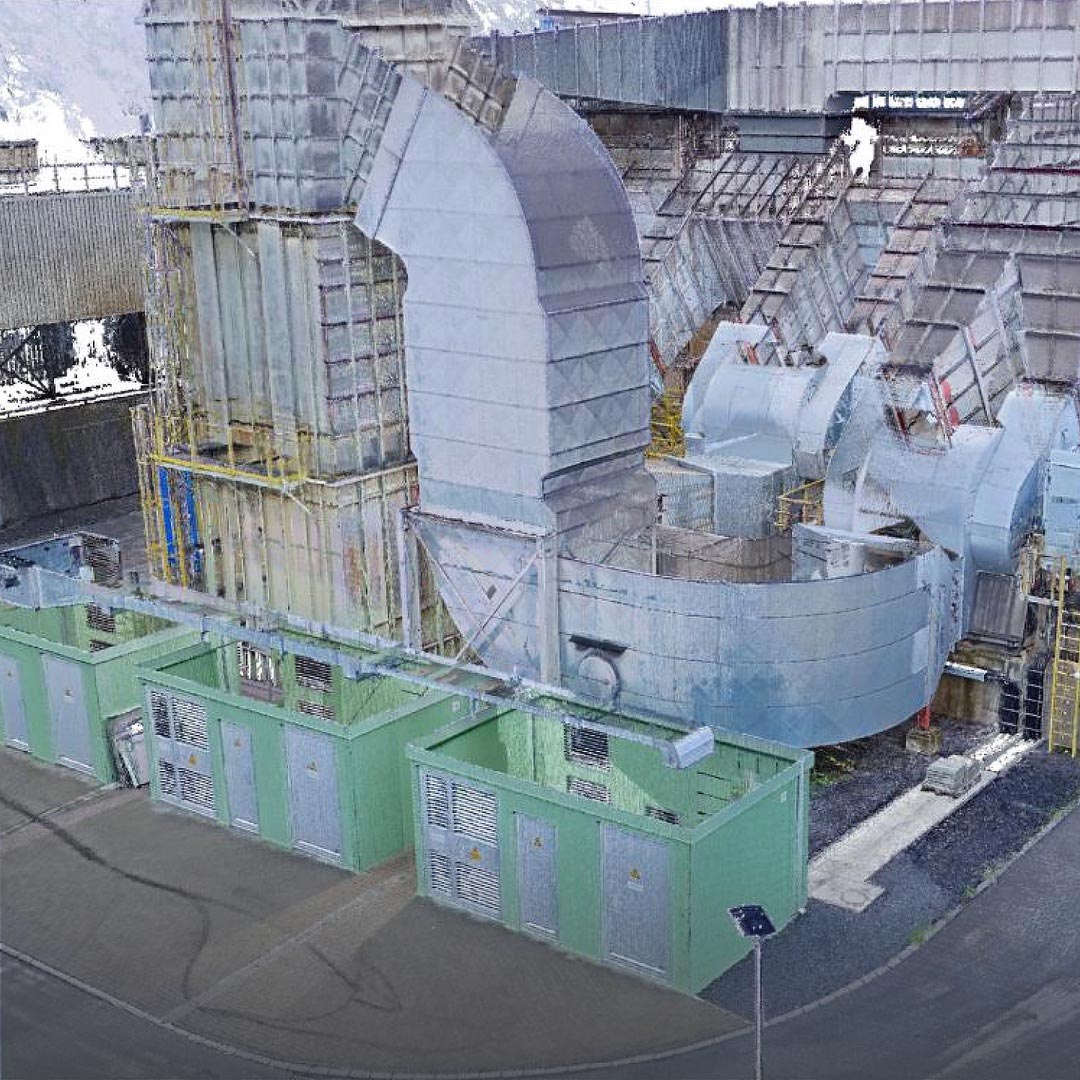
»We were able to implement the project as planned, the new system is in operation
and is running reliably. The quality achieved in all the important areas […]
is remarkably high and sets the tone for future projects..«
Project Manager Bernd Griesbach
Stahlwerk Thüringen GmbH
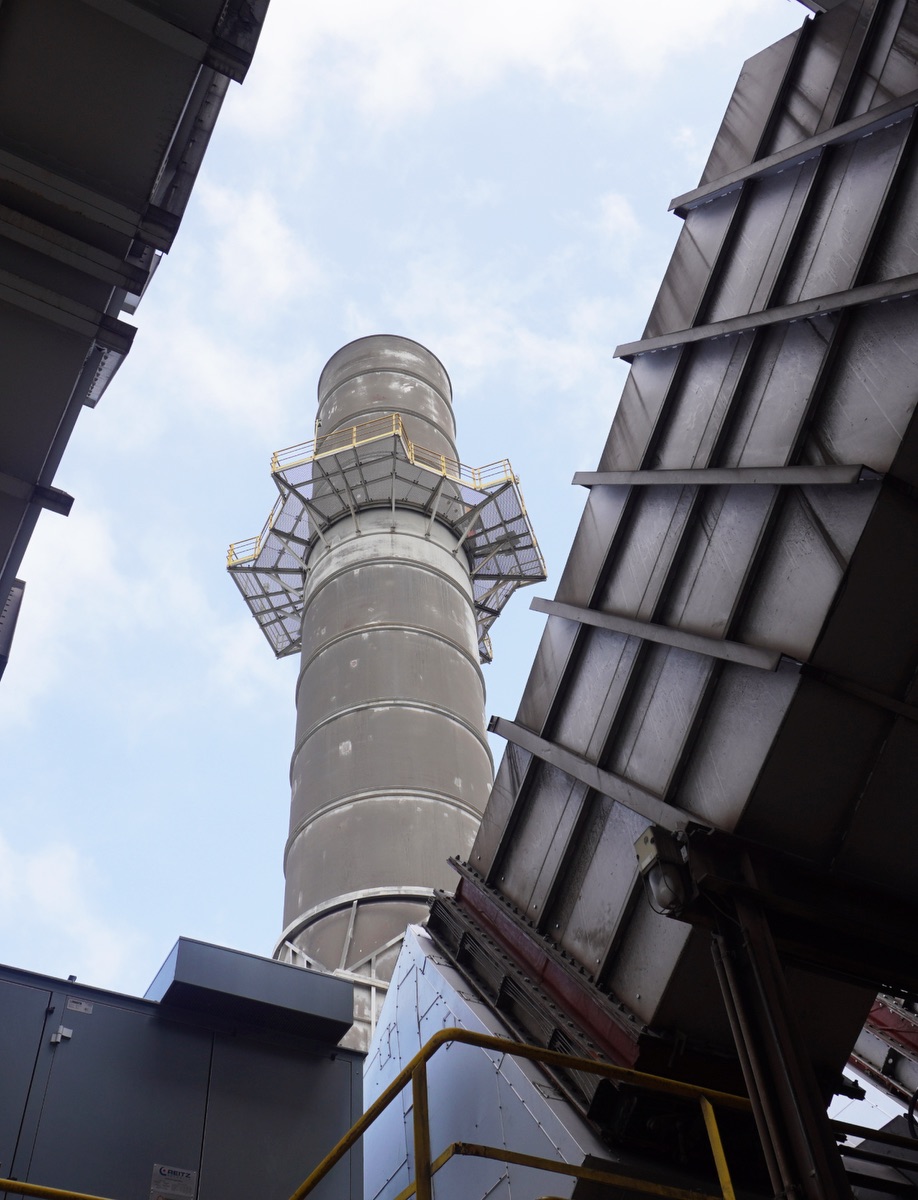
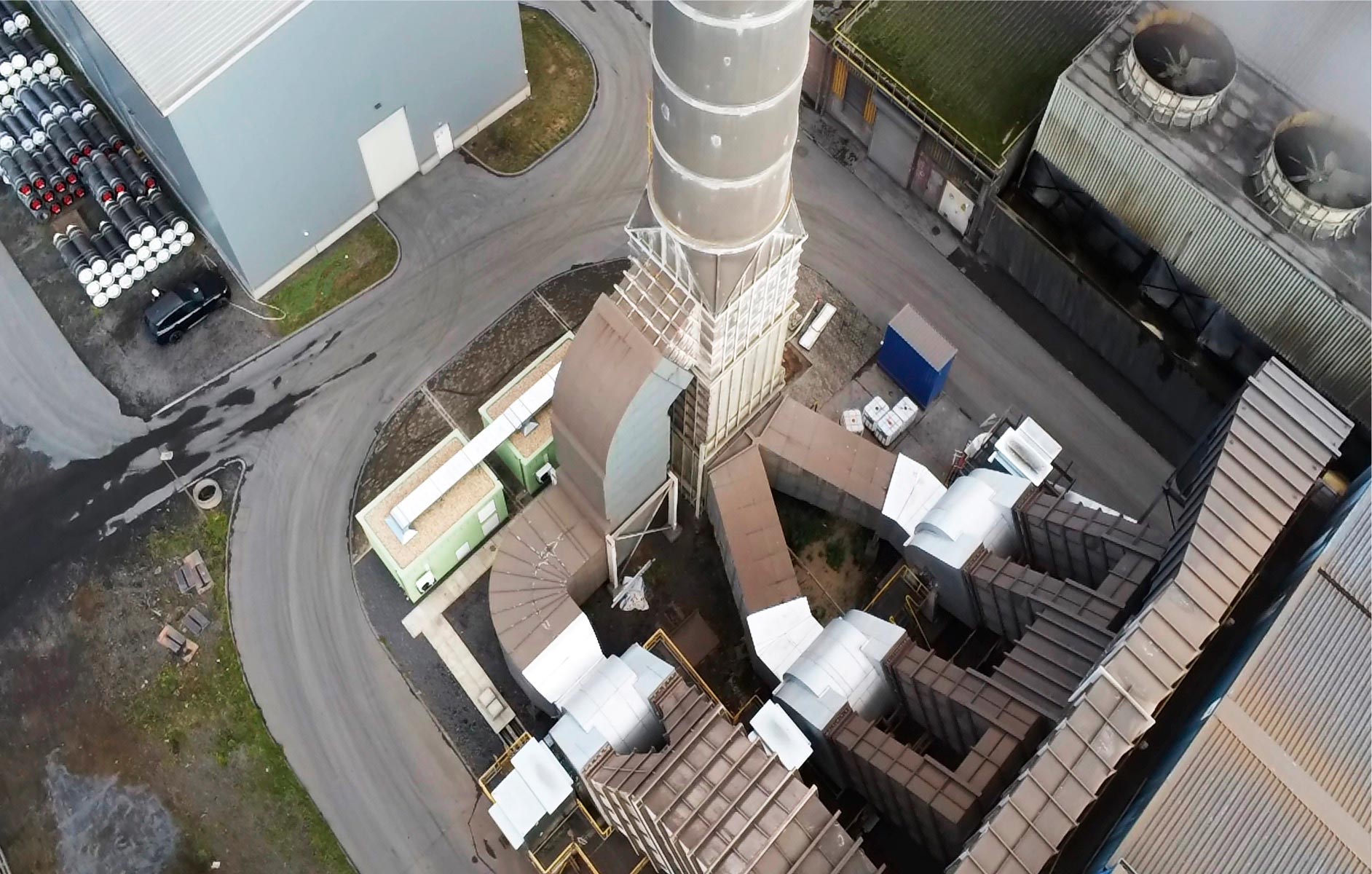
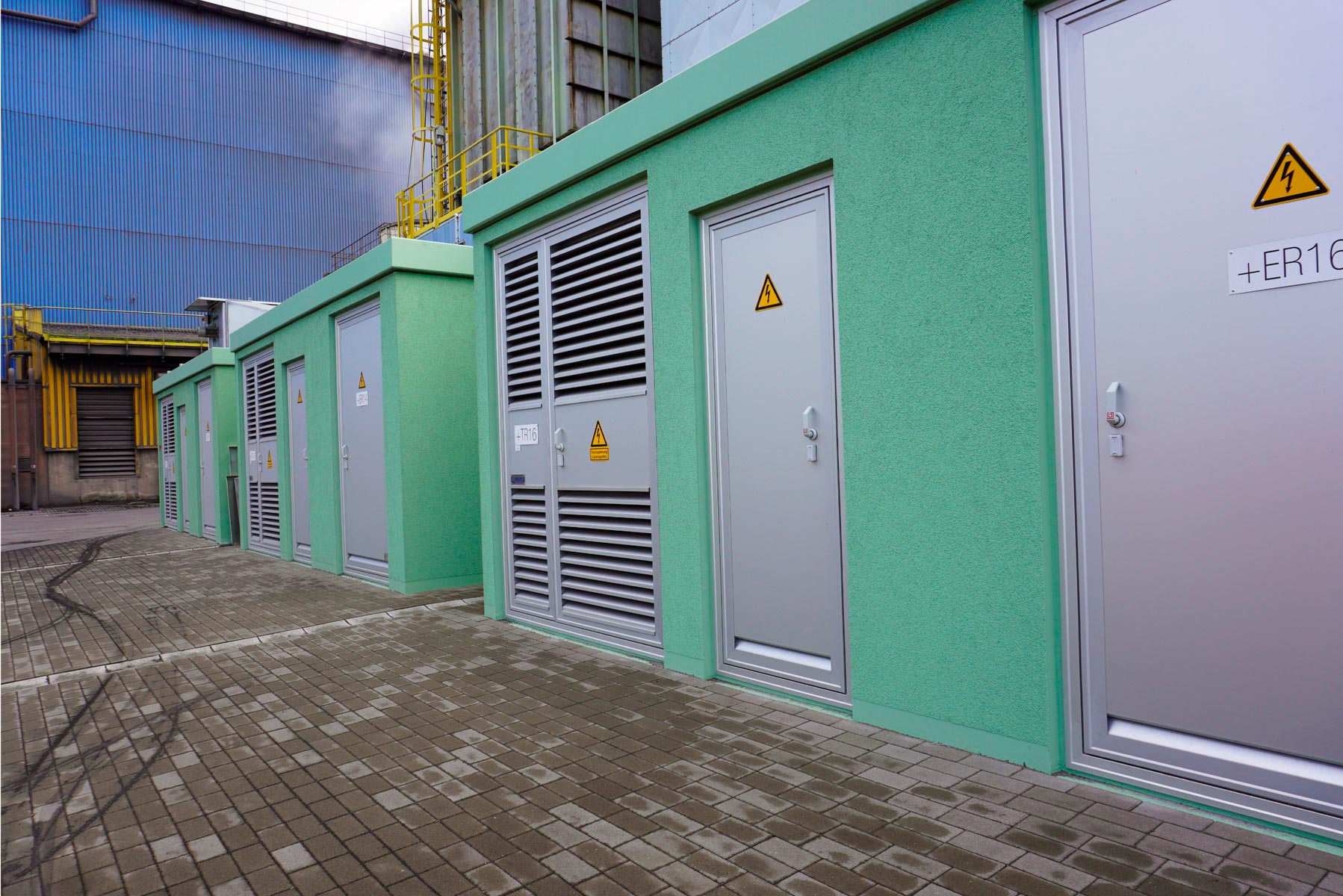
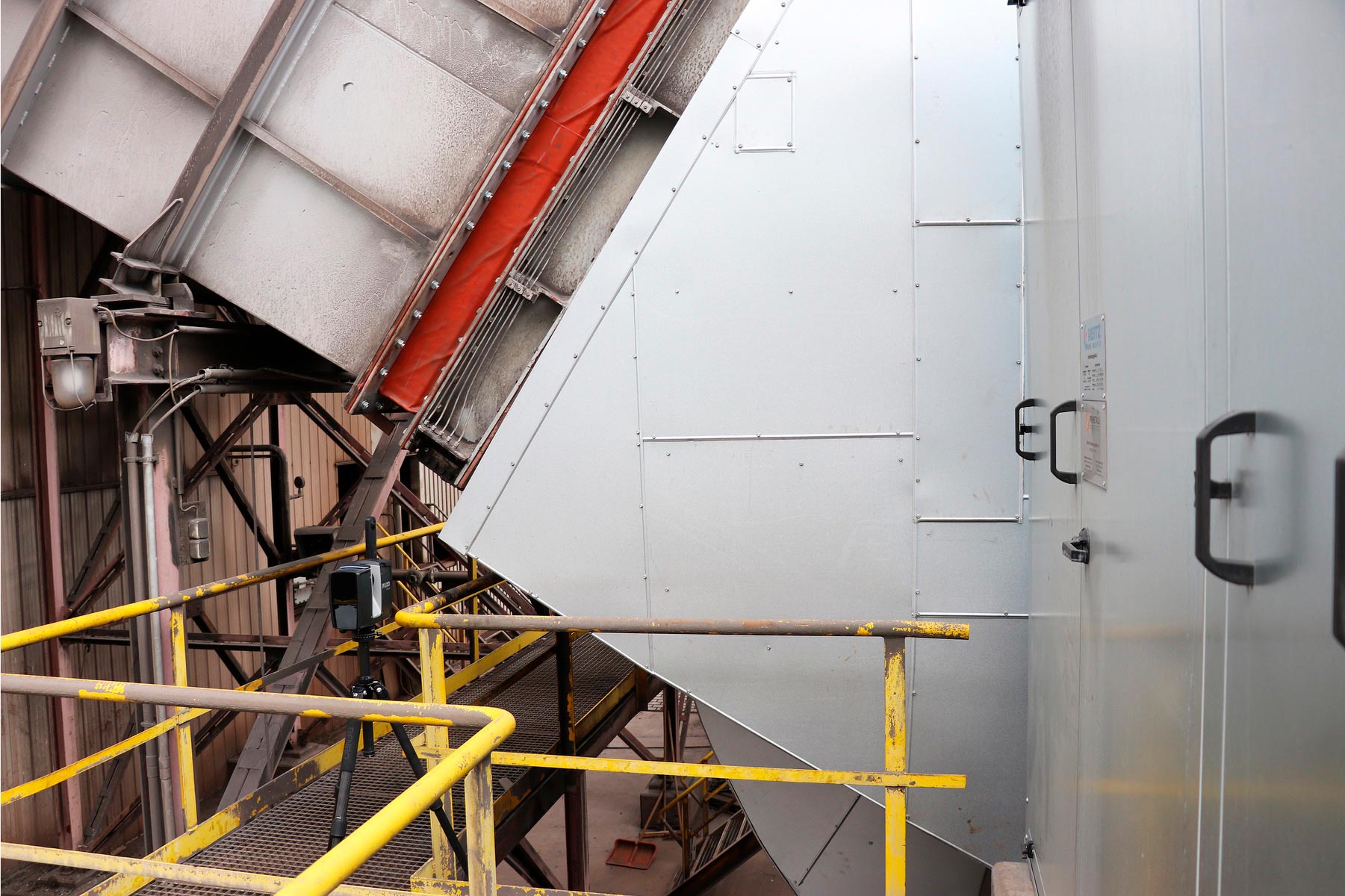
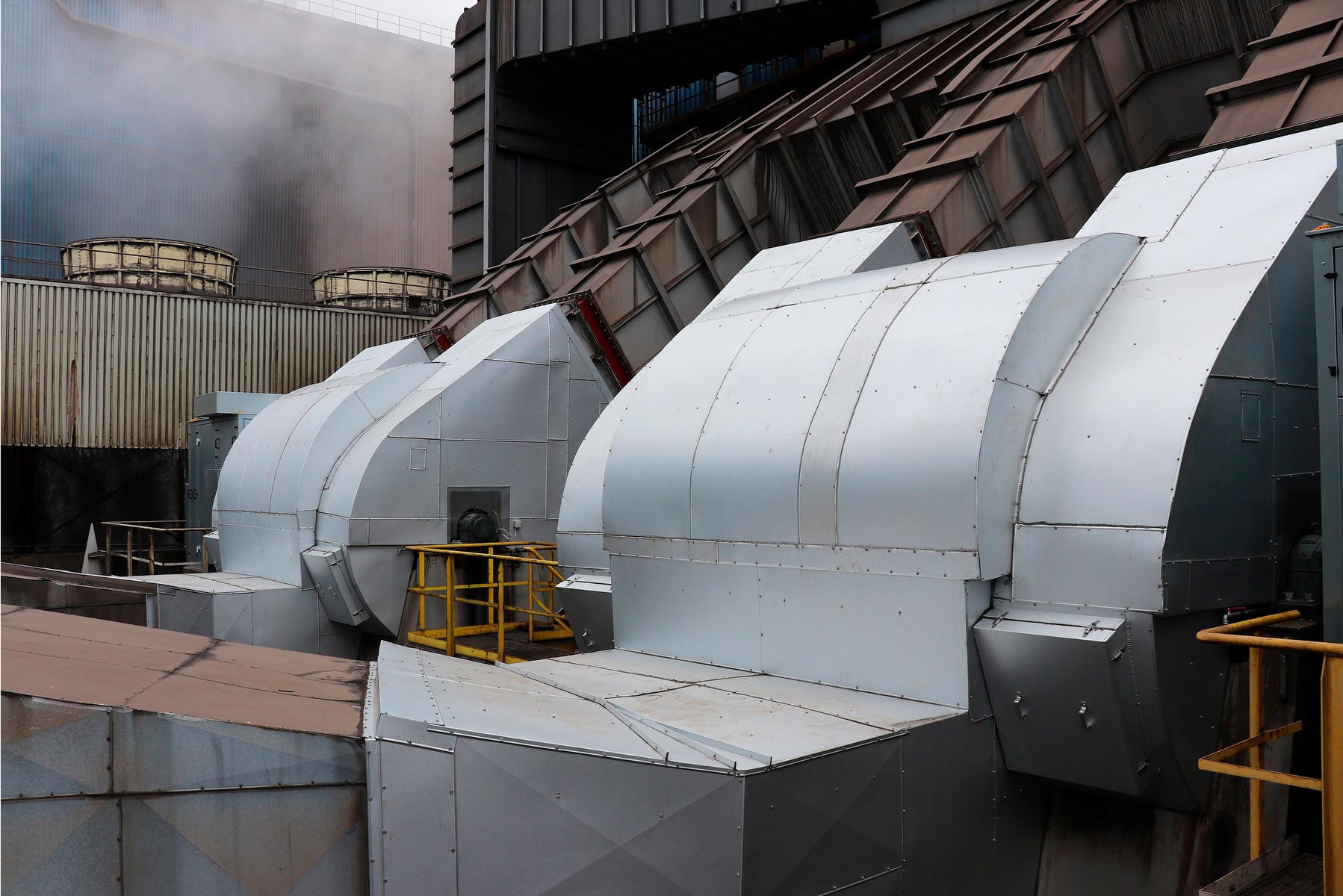
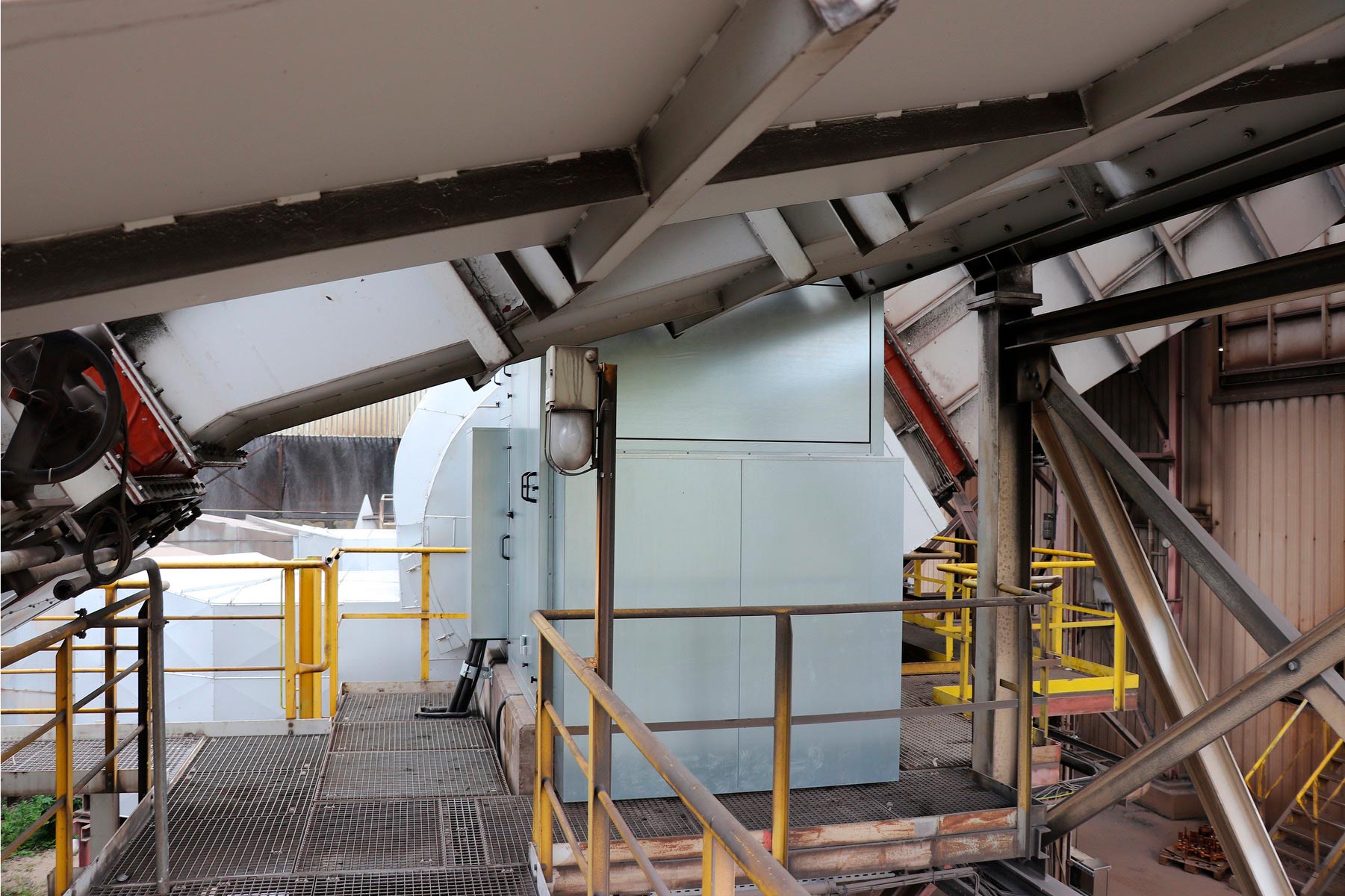
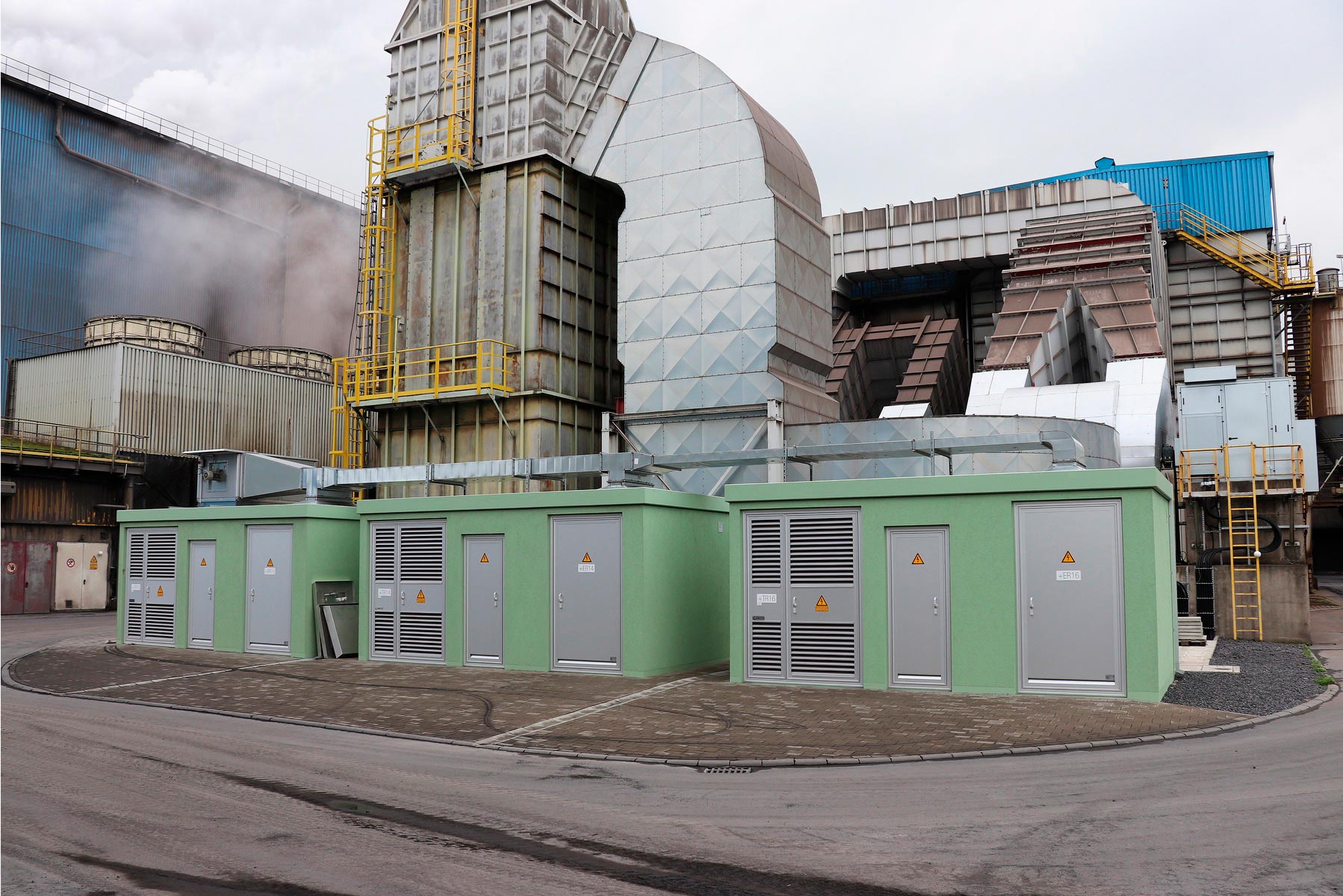
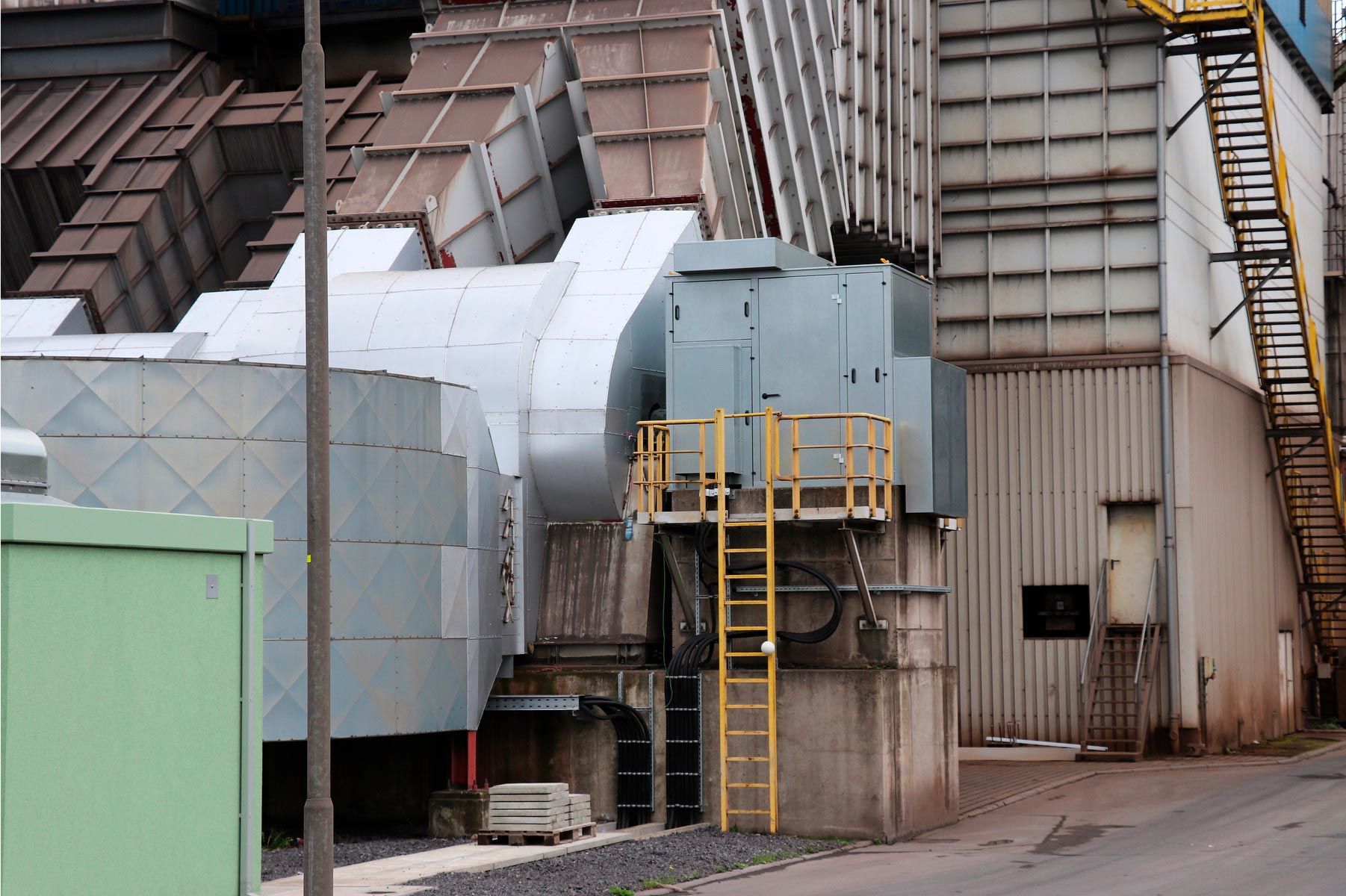
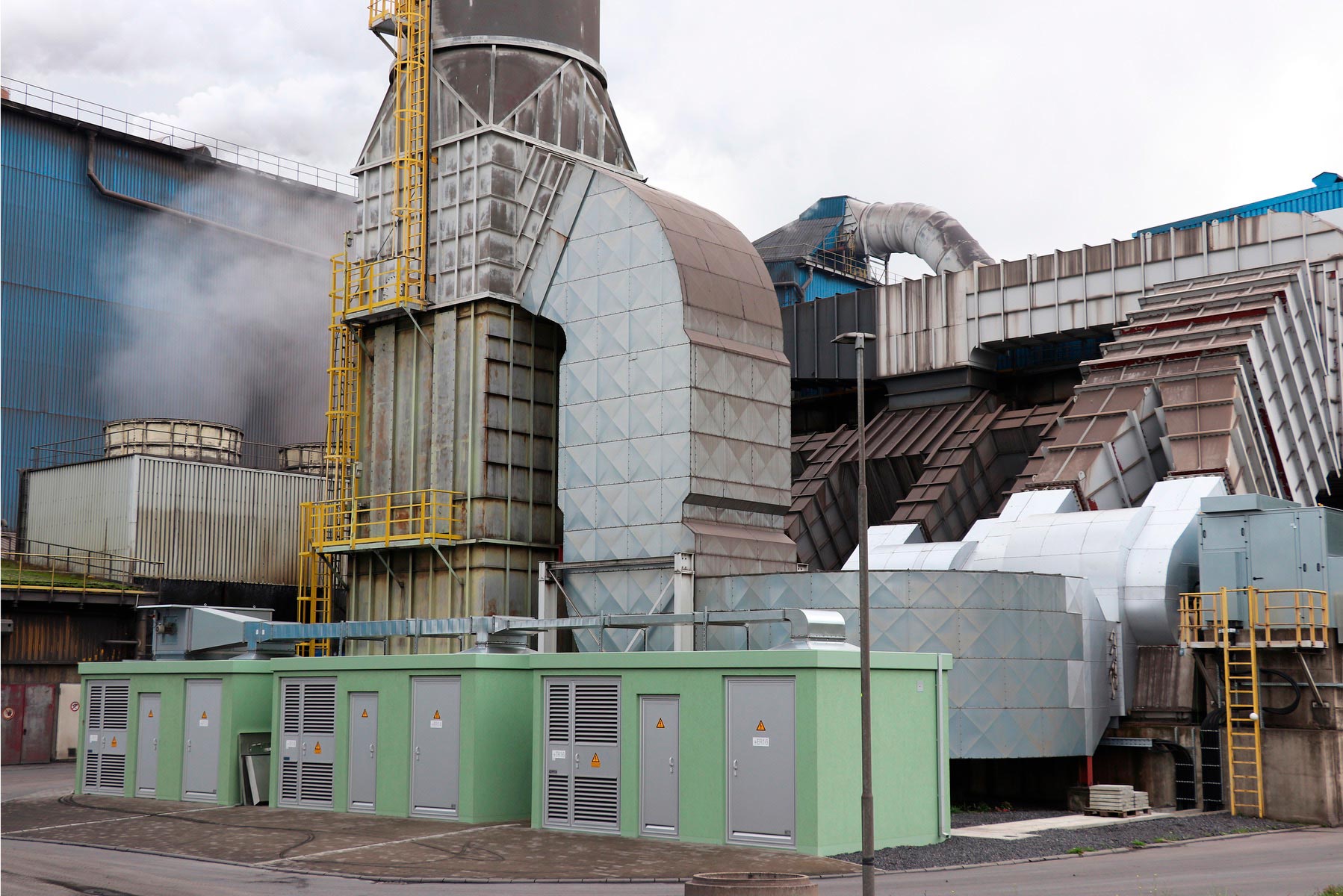
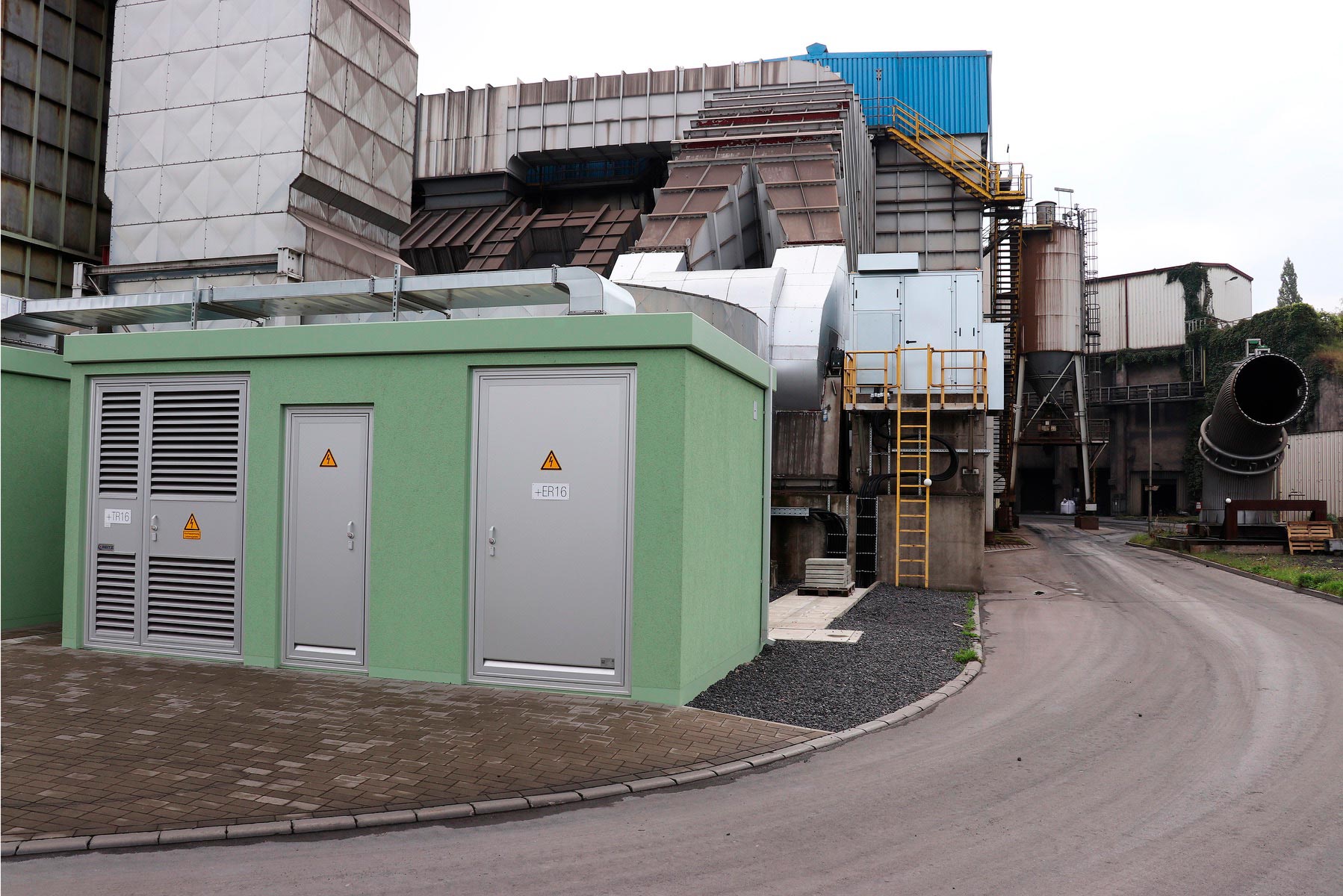
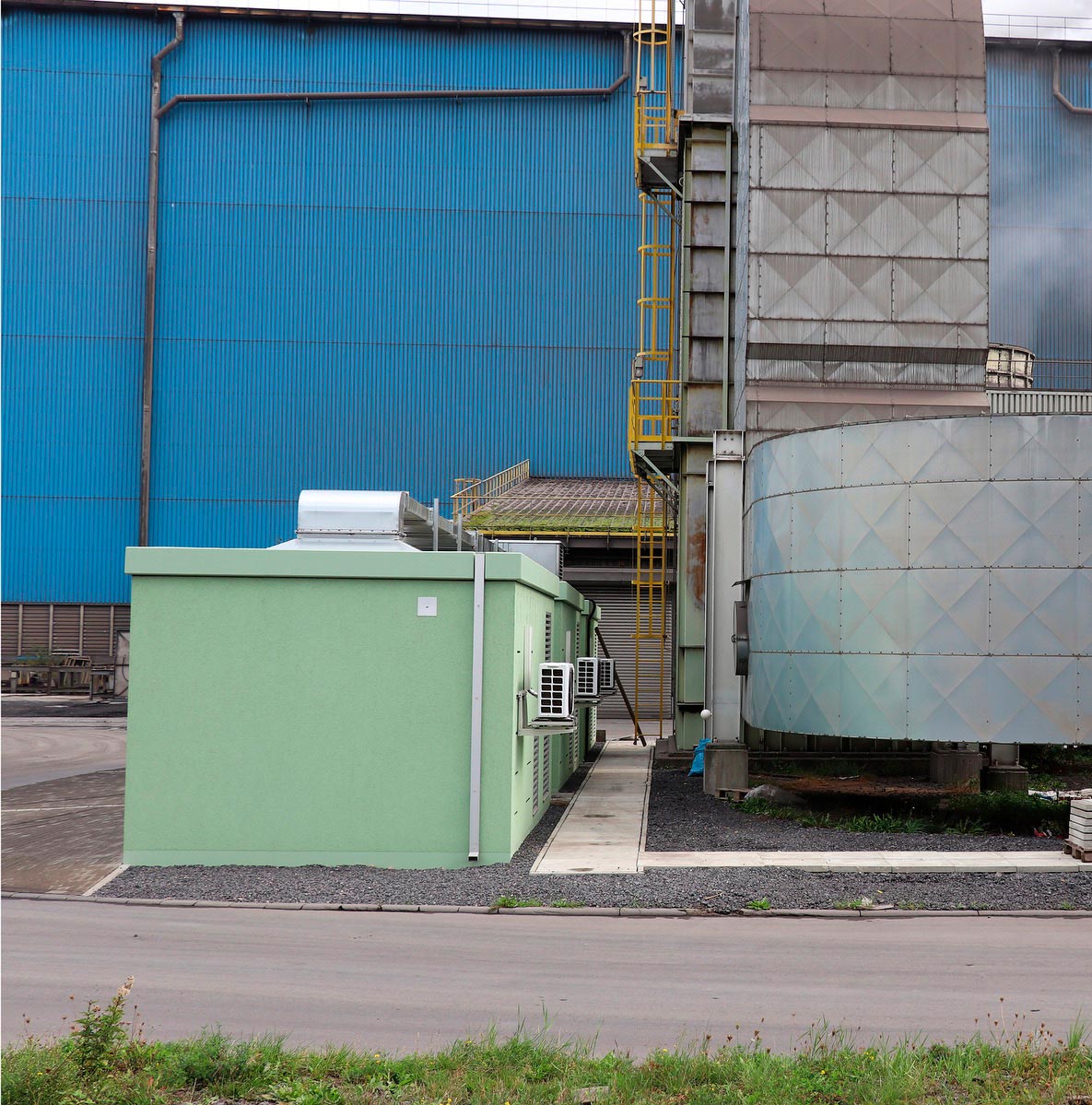
Conclusion
Advantages of the conversion
Thanks to precise planning, excellent teamwork and the use of state-of-the-art technology, the conversion was completed smoothly and on time. All work was successfully completed within the specified time frame of 8 days to full customer satisfaction and without any delays in the production process, which underlines our ability to achieve outstanding results even under demanding conditions.
- Up to 60% energy savings with the same output capacity
- Therefore short amortization time
- Reduction in CO2 emissions due to lower electricity consumption
- Fully automatic control of the fans
- Significant reduction in noise emissions
Initial calculations and operating experience have shown energy savings of around 45%, resulting in a short payback period – in addition to the CO2 emissions saved from the reduced electricity consumption.
Scope of delivery
- 3 x fan rotor units
- 3 x ow-voltage motors, 1250 kW each
- 3 x electrical rooms, each consisting of:
transformer, frequency converter,
voltage distribution, control system - Visualization
- Basic and detail engineering
- Dismantling and assembly
- Cable routes and cable laying
- Installation of new on-site control points
- Installation of sensors
- Coordination of all site work
- Commissioning of the entire system
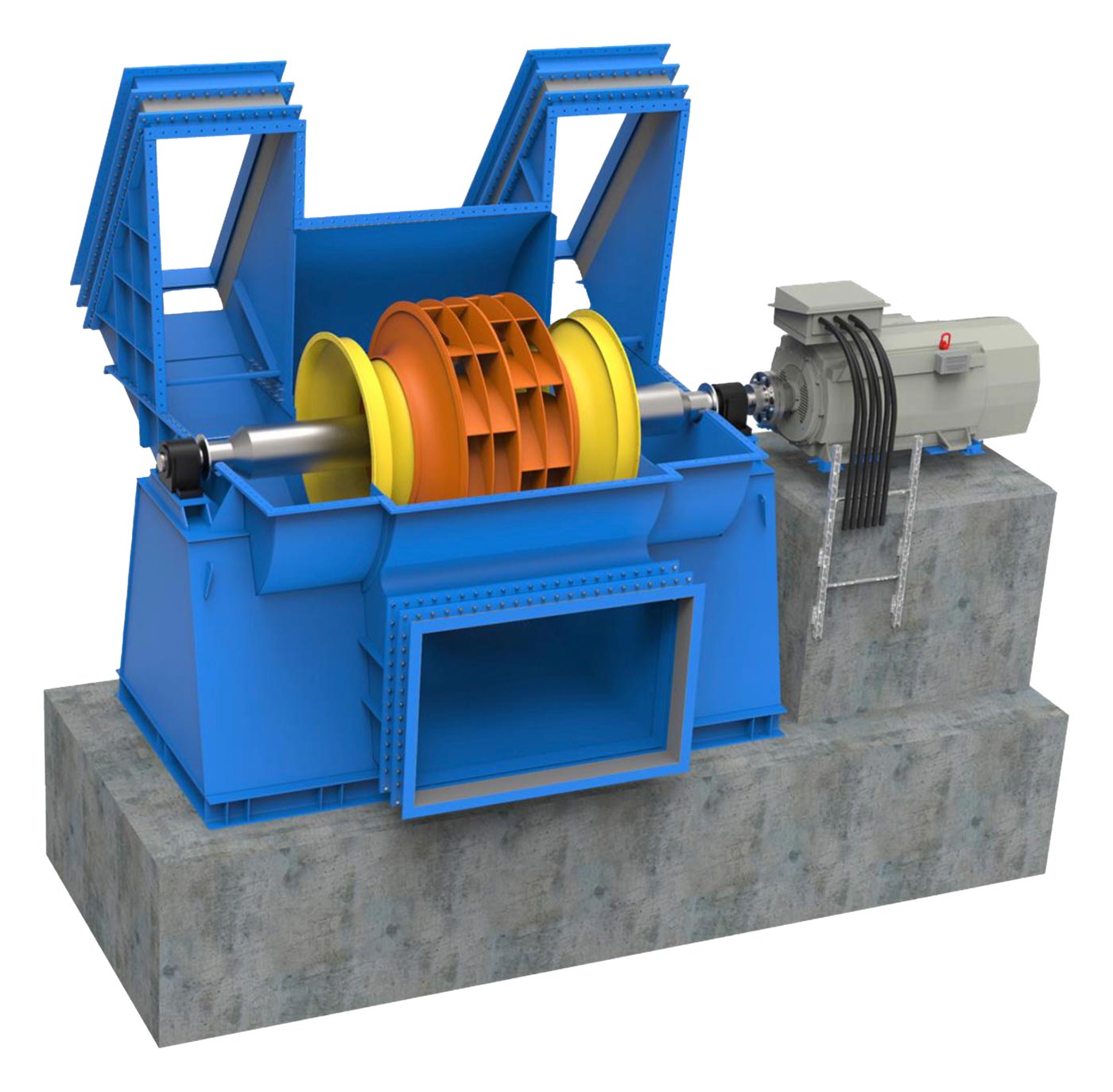